The Importance of Inventory Management in Order Fulfilment
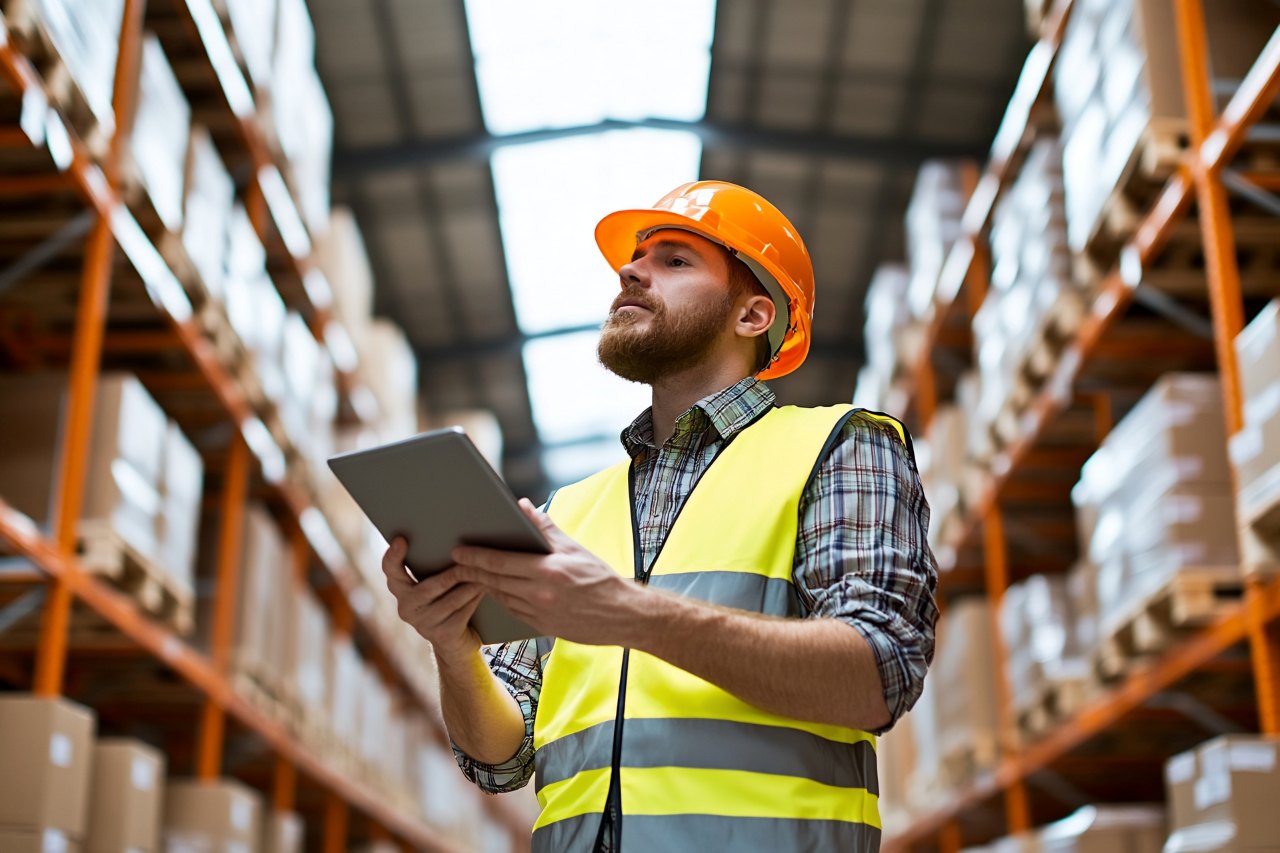
14/02/2025
Ever wondered why some online orders arrive the next day while others take weeks? Or why certain products are perpetually out of stock? The answer often boils down to inventory management, so let’s take a closer look at how it all works.
What Is Inventory Management?
Inventory management involves tracking stock levels, storage locations, and product movement throughout the supply chain. It's about having the right products in the right quantities at the right time—without tying up excessive capital in unsold goods.
For businesses handling physical products, inventory represents one of the largest investments. Managing it poorly leads to disappointed customers, wasted money, and operational chaos. Handling it well creates a seamless experience that keeps customers coming back.
The Connection Between Inventory and Order Fulfilment
Inventory and order fulfilment are two sides of the same coin. Order fulfilment is the process of receiving, processing, and delivering orders to customers. Inventory management ensures you have what you need to fulfil those orders efficiently.
When you're running low on stock, you can't fulfil orders promptly. When you're drowning in excess inventory, you waste storage space and risk obsolescence. Finding the balance takes skill, data, and the right systems.
If you're curious about where all this happens, you can read more about fulfilment centres and their role in the process.
Why Effective Inventory Management Matters
Preventing Stockouts and Overstocking
There's an art to inventory levels. Too little stock means disappointed customers and lost sales. Too much means tied-up capital, storage costs, and potential waste.
Stockouts can damage your reputation severely. About 70% of shoppers will go to a competitor if the item they want is unavailable. Even worse, many won't return to your store after experiencing a stockout.
Overstocking isn't any better. Excess inventory increases storage costs, risk of damage, and obsolescence. For seasonal or trendy products, overstocking can lead to significant losses when you're forced to heavily discount unsold items.
Enhancing Order Accuracy and Speed
When your inventory is well-organised and accurately tracked, orders are filled correctly the first time. Staff spend less time hunting for products or correcting errors, and more time processing orders efficiently.
This accuracy directly impacts customer satisfaction. Nothing frustrates customers more than receiving the wrong item or learning their order is delayed because of inventory mistakes.
Improving Cost Efficiency
Sound inventory management dramatically reduces operational costs. When you know exactly what you have and where it's located, you eliminate wasted time searching for products, reduce emergency shipping costs, and minimise storage expenses.
The financial impact extends beyond direct costs. Poor inventory management creates opportunity costs—tying up money in slow-moving stock instead of investing in growth, marketing, or product development.
Key Inventory Management Techniques for Order Fulfilment
Just-in-Time (JIT) Inventory
JIT aims to receive goods only as they're needed in the production process or for customer orders. This approach minimises inventory holding costs and reduces waste.
While JIT can significantly reduce storage costs, it requires excellent supplier relationships and accurate demand forecasting. When it works well, JIT creates a lean, efficient operation with minimal waste.
ABC Inventory Analysis
ABC analysis categorises inventory based on importance:
- A items: High-value products with the biggest impact on your business
- B items: Mid-range products of moderate importance
- C items: Low-value products that constitute the bulk of inventory but contribute least to profits
This approach helps allocate resources efficiently. A items get the most attention, while C items are managed with simpler systems.
FIFO and LIFO Methods
First-In-First-Out (FIFO) means the oldest stock gets sold first. Last-In-First-Out (LIFO) means the newest items go out first.
For most products—especially perishables or items subject to obsolescence—FIFO makes more sense. It ensures stock rotates properly and reduces waste. LIFO is typically used only in specific accounting or non-perishable contexts.
How Technology Enhances Inventory Management
Inventory Management Software
Gone are the days of clipboard inventory counts and Excel spreadsheets. Modern inventory management software provides real-time visibility across locations, automated reordering, and detailed analytics.
These systems integrate with your sales channels, automatically adjusting inventory levels as orders come in. Many also generate purchase orders when stock drops below predetermined levels.
RFID and Barcode Scanning
Radio-frequency identification (RFID) and barcode technology have revolutionised inventory tracking. These tools enable quick, accurate stock counts and movement tracking without manual data entry.
RFID, in particular, allows for scanning entire areas at once, making stock checks dramatically faster and more accurate than manual methods.
AI and Predictive Analytics
Artificial intelligence and machine learning now help predict future inventory needs based on historical data, seasonal trends, and external factors like weather or upcoming holidays.
These tools can identify patterns humans might miss and adjust inventory recommendations accordingly. They're particularly valuable for businesses with complex product lines or seasonal fluctuations.
Best Practices for Optimising Inventory in Order Fulfilment
Conducting Regular Audits and Stock Checks
Regular physical counts remain essential, even with advanced tracking systems. They help identify discrepancies between your records and actual stock levels before they cause problems.
Cycle counting—checking a portion of inventory on a rotating schedule—offers a practical alternative to full inventories that shut down operations.
Demand Forecasting and Seasonal Planning
Anticipating future demand helps maintain optimal inventory levels. Historical sales data, market trends, planned promotions, and seasonal factors all influence what you'll need.
For seasonal businesses, early planning is vital. Having forecasts ready well before peak periods ensures you can secure necessary stock without paying premium prices for rushed shipping.
Integrating Inventory with Order Management Systems
When your inventory system communicates directly with your order management platform, you eliminate manual updates and reduce errors.
This integration creates a smooth workflow from order placement to fulfilment, with real-time updates keeping everyone informed—from warehouse staff to customer service representatives.
Final Thoughts
Effective inventory management isn't just about counting products—it's about creating the foundation for excellent customer service and operational efficiency. When you know exactly what you have, where it is, and when you need more, you create a seamless experience for customers while optimising your operational costs.
Whether you're managing inventory in-house or working with fast ecommerce fulfilment solutions in the UK, focusing on accuracy, visibility, and continuous improvement will help you build systems that support your business goals and keep customers satisfied.